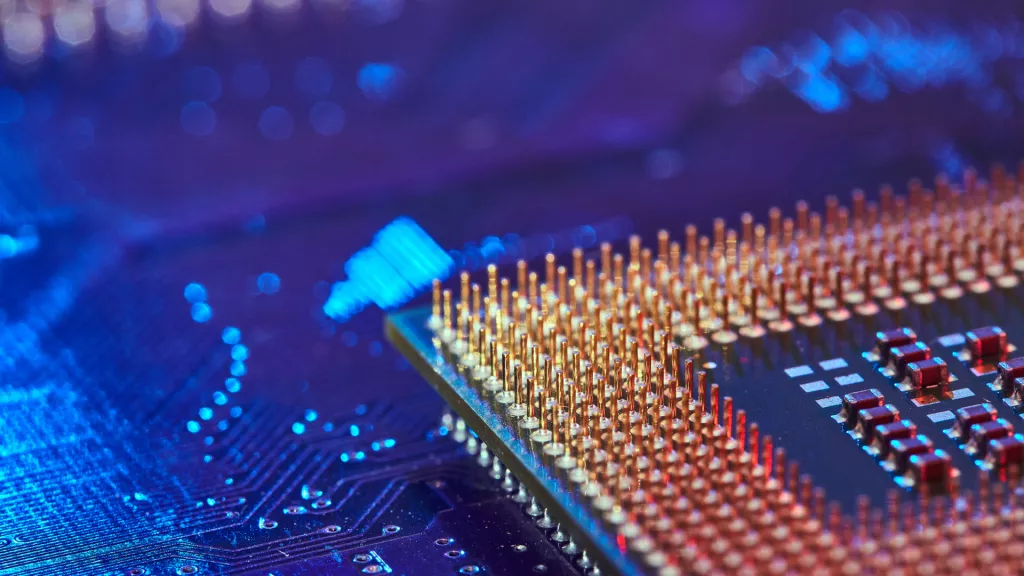
The chip shortage runs deeper than you think
Silicon chips are undoubtedly part of the machinery that makes the world go around, but in 2020, a combination of factors led the entire chip industry into trouble.
With Covid-19 rearing its ugly head and wreaking havoc, much of the world shut down – but Coronavirus isn’t the only reason for the issues that followed.
Poor planning was a major factor, as was competition between specific industries for the attention of the chip manufacturers, and even natural disasters had a role to play – in short, the global chip shortage is even more complex than you might imagine.
Primary factors
Looking back, it’s impossible to point to one or two reasons for the chip shortage, as it was a whirlwind of problems coming together at the wrong time.
But to begin with, there was a lack of incentive for silicon chip producers to build enough foundries to satisfy automakers and others, says Mario Morales, Program Vice President of the semiconductor group at analyst firm IDC. Morales claims nobody is investing in ”legacy technology”, which although dated, still plays a major role in many industries.
During the pandemic, original equipment manufacturers (OEMs) in the automotive sector “canceled orders from a lot of the supply chain,” he explained. “So, a lot of disgruntled suppliers found other markets that were still doing well despite the pandemic.”
But the problems can be traced further back. In the fall of 2018, for example, the United States placed trade sanctions on China. This led to Huawei, one of the biggest smartphone makers in China, placing huge orders for chips before these sanctions were implemented. Apple and others followed suit in a bid not to be left behind – and then the pandemic took hold.
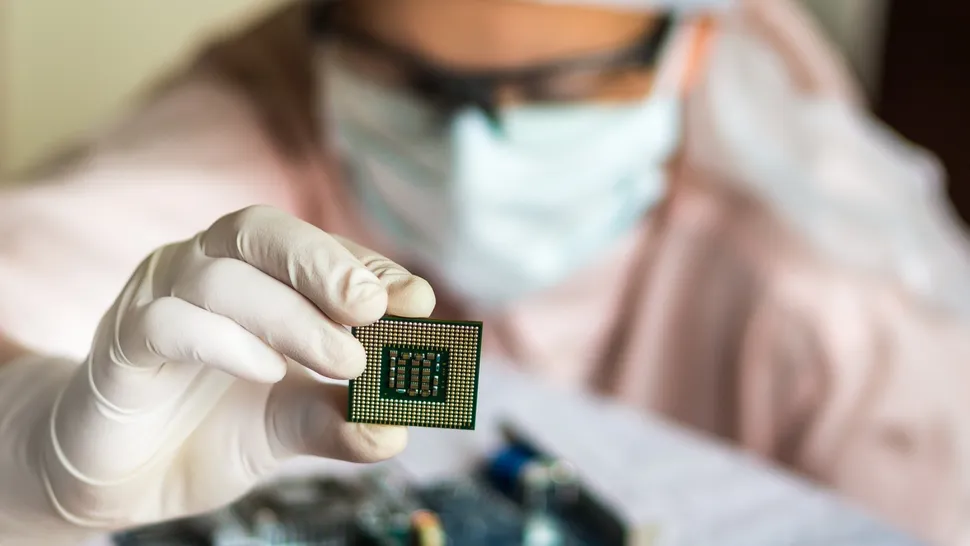
It’s no surprise that the pandemic lockdowns had a role in the silicon shortage, but it also affected other areas. Pretty much anything that has a battery or plugs into a wall uses chip-based technology.
For example, the demand for cloud computing services went through the roof as many consumers started purchasing products they typically wouldn’t need to work from home – with many businesses doing the same.
Smartphones remain the most popular electronic commodity in the world, so demand remained high, and crypto enthusiasts and entrepreneurs snatched up graphics processing units (GPUs).
What other factors contributed to the global chip shortage?
A number of other underlying factors also contributed to the chip shortage, with the complexity of items such as semiconductors also a significant factor.
According to Craig Barrett, former boss at Intel, the company’s microprocessors are the most complicated devices ever made by man. The process is so delicate that the rooms where semiconductors are built are cleaner than hospital operating rooms. In an operating room, they allow 10,000 particles of air pollution for one cubic meter of air. In a room where a semiconductor is built, they only allow 10 for every cubic meter.
So making silicon chips isn’t easy, but the people who do it are talented and backed by excellent resources. So, what’s the real problem?
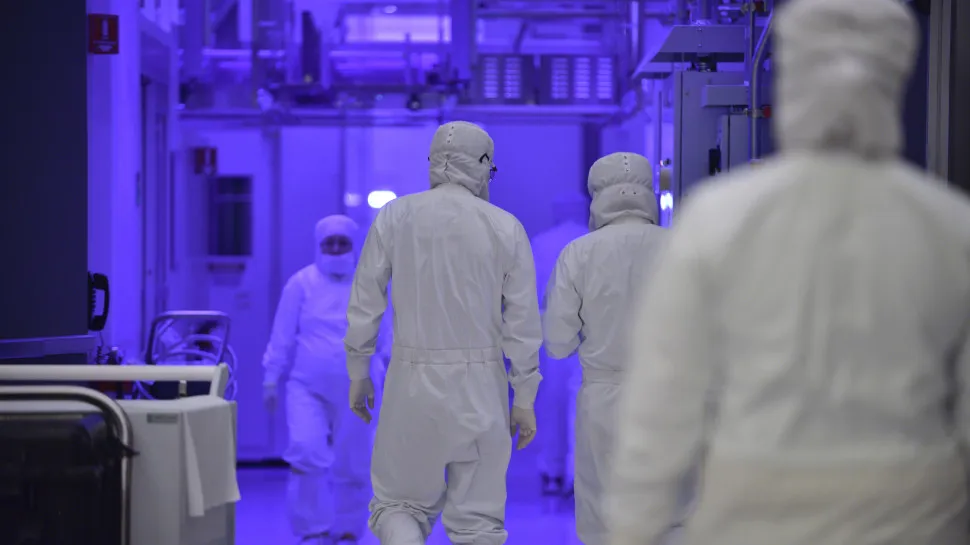
Whether it’s easy or hard to build a semiconductor, the fact is the process takes billions of dollars and a lot of time. And if you’re off by a fraction in the process, you’ll most likely lose out to another manufacturer.
Making a chip from start to finish takes about three months and involves million-dollar machines. There are also molten metal and lasers involved, as you’re taking a silicon wafer and turning it into a transistor to power your computer, smartphone or other smart device.
Finally, multiple factors outside of the semiconductor industry’s control also played a part. Power outages in Texas, where the majority of the United States’ chip manufacturing is done, and drought in Taiwan, also contributed to the shortage.
The world’s largest chip manufacturer, TSMC, also had to cut back its water usage (fundamental to the production of chips) due to government orders. Taiwan makes up over 60% of the world’s total global chip foundry revenue and the country wasn’t able to keep up its usual output.
What industries are most affected?
Automakers have been practically immobilized for over a year, and the situation might get worse. A new outbreak of Covid in South East Asia, where most US automakers’ chip manufacturing is done, could hit the industry even harder next year.
Production in countries such as Vietnam, the Philippines, and Malaysia was halted due to the outbreak, but US automakers rely heavily on those countries to keep their production lines moving since home-grown fabs only account for 12.5% of chip manufacturing.
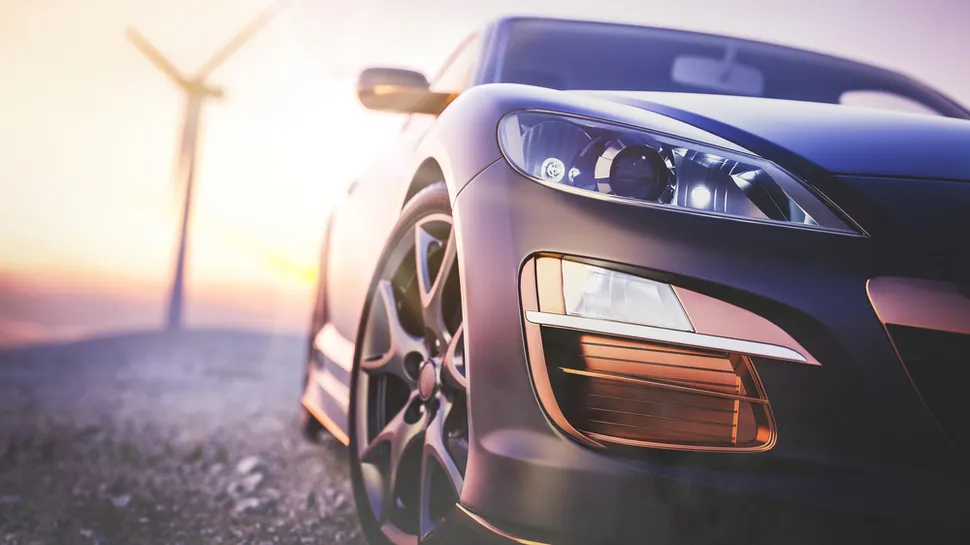
Another suffering industry is consumer electronics manufacturing. For instance, Hon Hai Precision Industry, an Apple supplier, said about 10% of its shipments would be affected. Xiaomi, meanwhile, said its smartphones would see a price increase because of the global chip shortage.
Apple’s MacBook and iPad products have also encountered production issues, and in March, Samsung announced its new Galaxy Note would indefinitely delayed.
The latest data shows smartphone sales have fallen 6% year-on-year, and this is because production has stalled, and in some cases, halted. On top of that, chip manufacturers are increasing their prices to prevent over-ordering – and whether that influences the price of smartphones next year remains to be seen.
Smartphone manufacturers like Samsung and Apple dodged the initial bullet of the microchip shortage, having seen what was coming a lot sooner than the automotive industry – although some issues are still arising.
However, the auto industry and others are catching up. Accenture’s Global Semiconductor Lead Syed Alem says, “smartphone companies benefited from the extra capacity left behind by automotive businesses, which led the automotive sector to experience a chip shortage when demand for cars rose faster than they anticipated.”
“Now that the automotive sector and others are catching up and starting to reclaim the capacity they had given up, there is fierce competition for semiconductor supplies. This has created supply pressure for smartphone chips.”
Due to pent-up demand and an improved consumer outlook, the first quarter of 2021 saw worldwide smartphone sales grow 26%. However, chip manufacturers are unable to meet the demand, and that probably won’t change by the end of the year.
Impact on price
Along with the possible price increase on smartphones, several other products have become more expensive as a result of the shortage.
GPU and CPU pricing has skyrocketed since the global chip shortage began, with the latter saoring to about 50% above MSRP in most markets according to some experts.
In March to May 2021 alone, the price of GPUs increased 14%, with Nvidia’s RTX 3060 and RTX 3080 GPUs are selling for quadruple their MSRP, and RX 6700 XT or RX 6900 XT going for double the MSRP.
There are three main factors that have contributed to the increase in GPU and CPU price hikes: scalpers, supply chain issues and distributors playing hardball.
We’ve already covered price rises, but for many manufacturers, there’s another reason for doing so: they want to keep scalpers from purchasing the GPUs at MSRP and then gouging the market.
Although they don’t control pricing for CPUs and GPUs, distributors are more or less forcing retailers to buy bundles of products. Simply put, they’re telling retailers a particular CPU or GPU is only available if they buy X,Y and Z along with it. In turn, retailers increase the price of the GPU or CPU to offset the additional products they had to pay for just to get the GPU/CPU they need. Or, you’ll see retailers trying to push bundles when customers need nothing of the sort – a trickle-down effect that isn’t helping the current chip shortage situation.
However, there’s more to it. Fabrication plants (fabs) have a limited amount of chips they can make and supply. Samsung and Taiwan Semiconductor Manufacturing Company (TSMC), which supply Nvidia and Advanced Micro Devices (AMD), respectively, can’t currently produce any more GPUs. Furthermore, there are ongoing problems with substrates, raw materials, GDDR memory, and components. That’s also why the price of GPUs has spiked more dramatically than CPUs.
Black Friday and Christmas
The holidays are fast approaching, and the global chip shortage will play a part in it. You can’t predict precisely what will happen with products for Black Friday, but there are strategies you can pursue to mitigate problems.
With Covid-19 still prevalent in Southeast Asia, where many goods are manufactured, you can expect shelves to be barer compared to years past. You can also expect prices to continue to rise for just about everything due to a lack of manpower, supply shortages, and longer shipping times.
Commentators also predict the price of goods will continue to rise through the end of 2021, with typical Black Friday sales and promotions set to be scaled back across many retailers.
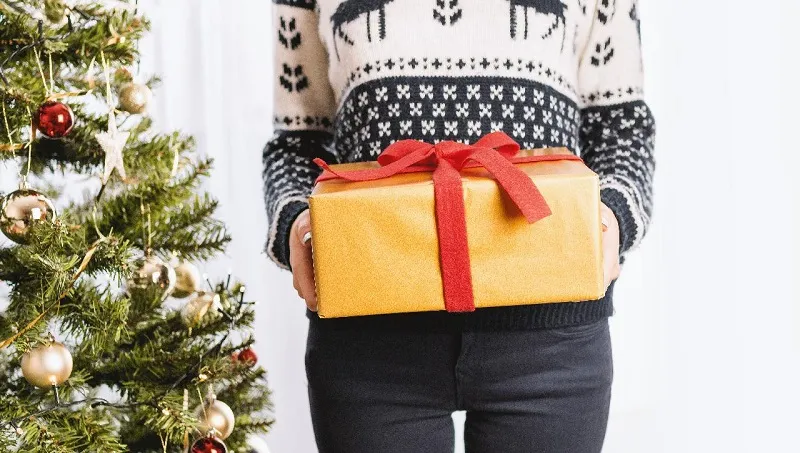
Christmas will likely also be affected, with retailers facing issues in stocking shelves with children’s toys, especially those with electronic chips. According to the Head of Sky Castle Toys, Lev Nelson, aside from the chip shortage itself, toy companies are often pushed to the back of the semiconductor line by higher-margin items such as cars, smartphones, and washing machines.
To avoid getting price gouged on or before Black Friday and Christmas, you should start shopping now. The sooner the better, especially for anything that uses a silicon chip.
What other products are affected?
According to Goldman Sachs, the global chip shortage has touched 169 different industries. Any industry that spends at least 1% of its GDP on semiconductor chips is adversely affected – with the auto industry spending nearly 5% of its GDP.
One other area that has been particularly affected acutely is telecoms. Telecommunication carriers have struggled to fill orders since the chip shortage began, as have satellite and telecommunication resellers, along with internet publishing, broadcasting, and web search portals.
In the wholesale trade sector, professional and commercial equipment supplies have also taken a big hit, with companies unable to fulfil orders due to supply chain issues.
Used cars and rental companies have also had to make adjustments due to the chip shortage, as for the first time in 68 years of tracking, used cars saw their first yearly price increase, with prices rising almost 10% in 2021.
When might the chip shortage end?
While many predict the global chip shortage will likely end sometime in 2022, Intel CEO Pat Gelsinger expects it won’t end until 2023. In an interview with CNBC, Gelsinger said, “we’re in the worst of it now; every quarter next year, we’ll get incrementally better, but we’re not going to see supply-demand balance until 2023.”
However, AMD CEO Lisa Su thinks the shortage will end sometime in 2022. She said production will be tight, “[but will get] better next year, not immediately, but it’ll gradually get better as more plants come up.”
Gelsinger stated that it isn’t only a lack of chips but a “combination of parts.”
“We call it match sets, where we may have the CPU, but you don’t have the LCD, or you don’t have the Wi-Fi. Datacenters are particularly struggling with some of the power chips and some of the networking or ethernet chips,” he explained.
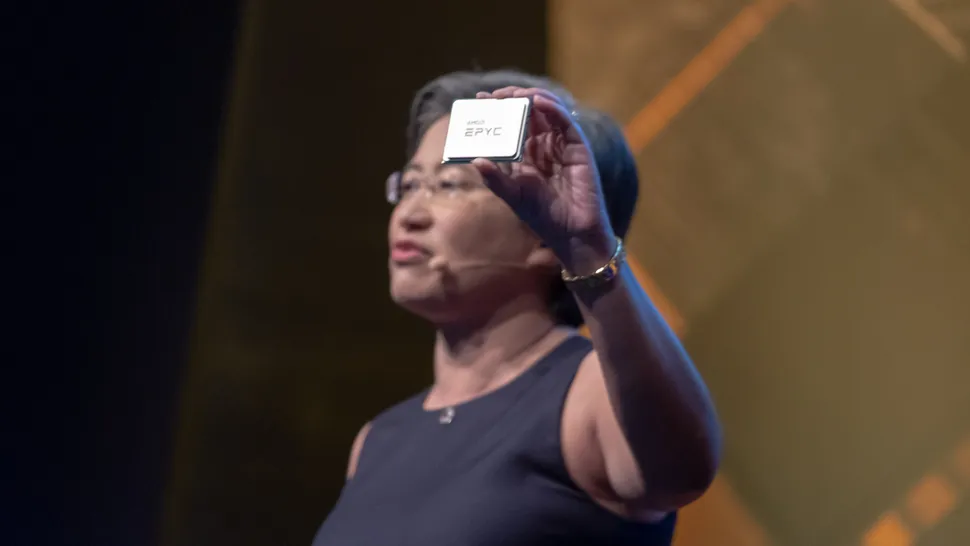
One way the global chip shortage might be solved is by the Internet of Things (IoT).
IoT technology can collect data and use it to prevent future chip shortages, with a chip fabrication plant that has “smart” connected equipment able to use real-time data allowing all members of its production team to make informed decisions that will reduce waste, speed up delivery times and increase product quality.
Next-gen innovation can also play a role, as the GaN semiconductor platform, for example, will be 3x lighter, 3x smaller, with 3x faster charging – with a combined effect of a 40% saving on energy costs.
Diversifying supplier bases can also help to mitigate the chip shortage or prevent it in the future. Creating strategic relationships with distributors, resellers, and traders can help when extra chips are needed in urgent situations.
What will happen to the chip manufacturing industry?
In the coming years, there will be a mixing of technologies, from 200mm (mature/legacy technology) and newer 300mm (for cutting-edge chips).
Pursuing only one of these avenues might keep the chip shortage going even longer – but building more 200mm fabs and 300mm fabs will get us out of the woods.
In 2020, there were 212 200mm fabs, with are a total of 222 expected by 2022. There were 129 300mm fabs in 2020, and experts expect a total of 149 to be live by 2022, with this growth trend expected to continue over the next decade.
The $52 billion US Innovation and Competition Act should also help funding by providing subsidies to chip manufacturing companies – if it passes through Congress, as well as the Biden Executive Order signed on February 24 2021.
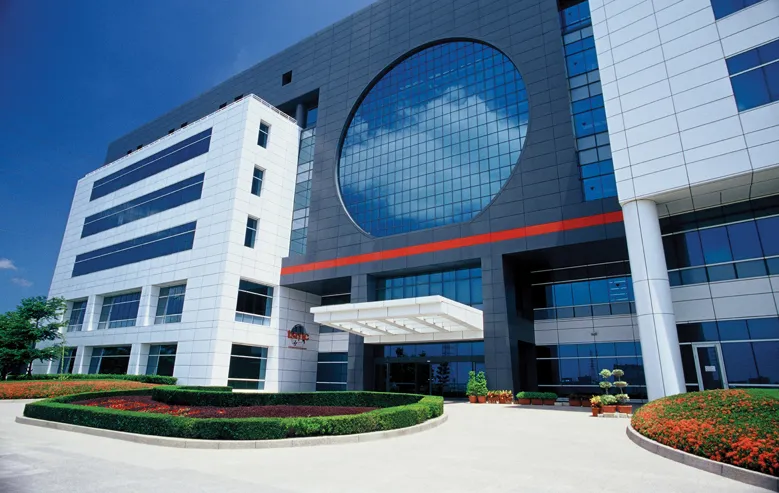
Finally, there’s the ongoing trade war between the US and China, which sees semiconductor chips as a crucial pawn.
In September 2020, former President Donald Trump imposed import restrictions on Semiconductor Manufacturing International Corporation (SMIC), China’s largest chip firm, forcing China to source parts elsewhere and rework its supply chain, causing a big slowdown in imports of chips to the US and elsewhere.
What does this mean for national security?
“[The chip shortage is] a challenge to the supply chain that could create threats to the very security of our nation,” Matt Hayden, former Assistant Secretary for Cyber, Infrastructure, Risk, and Resilience of the US Department of Homeland Security, told Kitco News.
According to Hayden, US information systems, defense systems, and sensitive electronics are what the government uses for homeland security, with all these affected by the shortage.
Shipments of semiconductors are being help up over 200 days. “We’re looking at days from 200 to past a year for specific chips that range from consumer electronics to major manufacturing across the world,” said Hayden.
An anonymous source told a Fox News Investigative Unit that whoever wins the race for the next generation of semiconductor products will have an extremely strong military, become a global economic force, and possibly dominate the geopolitical landscape.
There are also thoughts that China may try to take over Taiwan, which is the largest chipmaker in the world, accounting for 63% of Asia’s chip manufacturing production. If China did attempt and succeed in a military takeover of Taiwan, it would hold the key to the future of the modern world.
Where do we go from here?
It’s been over a year since the first signs of the global chip shortage, and companies across multiple industries have been affected, and will continue to be in the coming weeks and months.
Barring any more natural disasters, like droughts and severe winter storms cutting power, supply should start to turn around early in 2022 – but the overall situation doesn’t look like it will return to normal by the end of next year, or by the start of 2023. Some steps can be taken to turn the ship around or at least mitigate it from sinking further, and those measures are at our disposal.
We don’t know exactly what the future holds, but the global chip shortage will end at some point. It’s just going to last longer than anyone initially thought.